Preventing metal corrosion is essential to ensuring service life. Whether carbon steel or stainless steel, aluminum, bronze, copper, cast iron, magnesium or titanium-corrosive processes vary, chemical or electrochemical, and can manifest in some of these ways:
- Fretting- visible corrosion that includes pitting, grooves and debris relating to oxidation-the result of intimate contact between two opposing metal surfaces under an applied load in motion, often vibration.
- Galvanic- visible corrosion that includes pitting at the result of dissimilar metals each corroding concurrently, but at rates faster or slower than the other and differently than they would alone. Not to be confused with coupled metals exhibiting increased decay which are based on differences in electromotive force (EMF) potentials
- Other- corrosion may also include stress, hydrogen embrittlement, inter-granular, bacterial, and exfoliation.
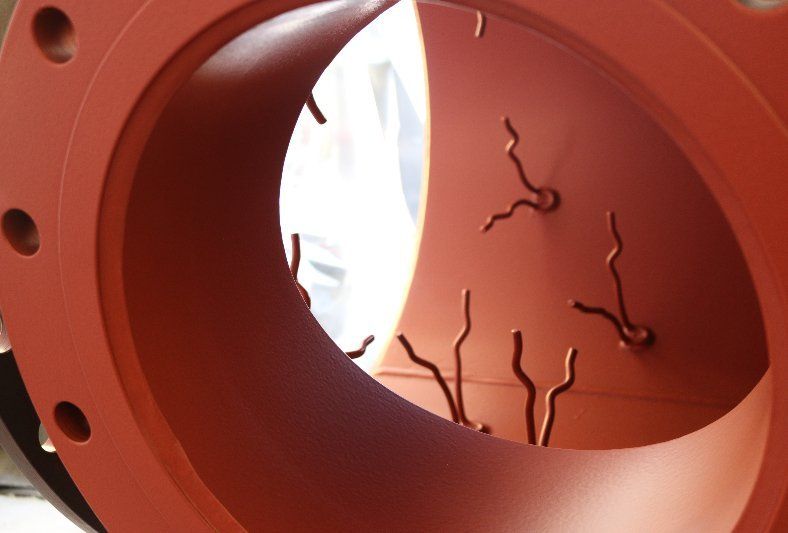
Coated with Ruby Red for corrosion resistance.
Prior to coating with corrosion.
HALAR®ECTFE is one of the more chemically stable fluoropolymers today. It is used to protect metal surfaces from highly corrosive environments. For the manufacture of high-purity fluids, such as pharmaceuticals or semi-conductors, where surfaces must be smooth, chemically-inert and resistant to bio-fouling, HALAR® resists corrosion and will not contribute to contamination.
Mechanically, HALAR® is tough, resists cut-through, offers excellent protection from abrasion and is stable dimensionally over a broad range in termperature from cryogenic to 150°C (300°F). Impact strength is excellent at both room temperature and cryogenic. Low cold flow is demonstrated.
The ECTFE fluoropolymer HALAR® is hydrophobic (resists wetting) and exhibits release (non-stick) properties. Its very smooth finishes resist microbial or bacterial corrosion and is unaffected by most chemicals today. These include: oxidizing agents, strong mineral acids, alkali's, high ph or low ph, metal etchants, de-ionized (DI)water, salt water or brine, ammonia, chlorine, sulfuric acid, liquid oxygen, and most organic solvents.
Additionally, HALAR® corrosion resistant coating is non-flammable and exhibits stability in UV light and weather, as well as resistance to high energy radiation.
HALAR® is a powder coating process, which offers numerous advantages over solvent-based coatings. Thicknesses, for example, as low as 0.2 mm to as high as 2 mm are attainable.
Bake cycles required to cure the coating remain comparatively low, between 250°C (482°F) and 290°C (554°F), which is beneficial for metals susceptible to distortion.
*** Halar® is a registered trademark of Solvay Specialty Polymers.